The P3 approach includes preventive, lifecycle maintenance for the asset and avoids the problems associated with deferred maintenance. Simply put, deferred maintenance is the practice of postponing infrastructure maintenance activities, usually due to lack of available funding. Lack of proper and timely maintenance leads to early deterioration that costs more to repair later on or shortens the lifespan of the asset. Both of these situations will cost extra over the long term as the asset will have to be replaced well before it was planned, resulting in unanticipated capital costs.
What is the remedy?
Government agencies can participate in a P3 project delivery structure that involves the agency partnering with a private entity to design, build, finance, operate and maintain an infrastructure project. A P3 allows a government agency to mitigate the risks and costs associated with maintenance activities by requiring the builder to maintain the project for the long term drawing funding from a fixed, known payment structure negotiated before the job is even started.
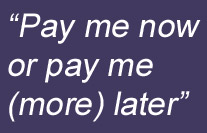
How exactly does this solve deferred maintenance?
Annual vs. lifecycle budgets
- Public agencies generally budget on an annual cycle. A private company utilizes longer term budgets and can “roll over” cost savings into later years. Snow removal is a good example: Savings in a “light” year will be sequestered and used in later years during an inevitable “heavy” year.
- Annual budgeting usually means that savings is “lost” in that year and the money is used for other priorities which may not be related to the subject asset. More importantly when the “heavy” year causes the budget to be expended, other repairs will likely be deferred resulting in an asset in poor condition and likely higher repair cost later as the asset continues to deteriorate.
Resource leveling
- Aside from a basic level of manpower and equipment for day-to-day tasks such as litter removal and incident management, many specialist tasks will be outsourced.
- Typically, government agencies will procure equipment and sometimes manpower that only has limited usage, for example tractors for mowing or bucket trucks for lighting repairs and their associated crews. The equipment is expensive but may only be used a few times per year. An outsourced contractor will perform the work, then move on to other unrelated projects. The asset only pays for what is used at the time and avoids expensive capital expenditures for equipment that sits idle.
Handback requirements
- To avoid having to rebuild or replace an asset prematurely (or at all), preventive maintenance is performed at optimum intervals to ensure the structure meets or exceeds its expected service life. The cost to clean, paint or repair assets periodically is far less than replacement cost if the asset doesn’t last as long as planned.
Conclusion
Using the P3 procurement method allows a private company to construct, service and maintain the asset which allows the government agency to save money through private company efficiencies, risk and responsibility allocation, and a firm funded budget.